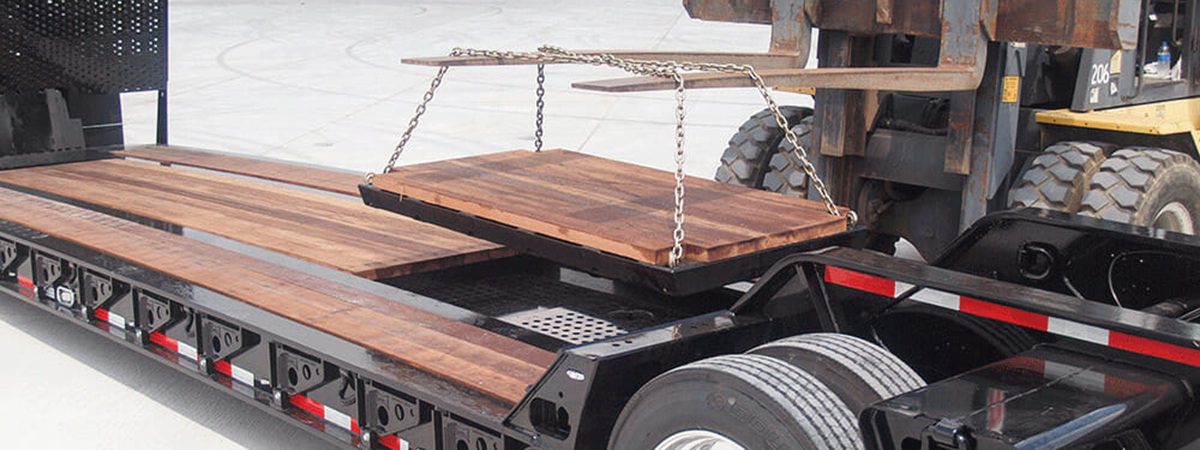
Preventative trailer maintenance on your industrial flatbed trailer can keep your rig rolling down the road. By performing regular checks to catch and fix defects before they become problematic. This early intervention makes sure your deliveries stay on time. It also avoids service delays caused by unexpected downtime and fix-it tickets from roadside inspections.
In today’s blog, we are going to look at the 10 most common areas to address. These tips of all types of trailers including your lowboy, dropdeck or traveling axle trailer. Some tips should already be part of your daily inspection routine. Others may occur during PMs, and some need to be completed at other regularly-scheduled intervals.
Find the schedule that works the best for you and your fleet’s operation. The key takeaway here is to not ignore issues or put off routine maintenance. Preventative maintenance measures can ultimately save you time and money and preserve your reputation as a dependable carrier. Let’s start our rundown where the rubber meets the road.
1. Wheel torque
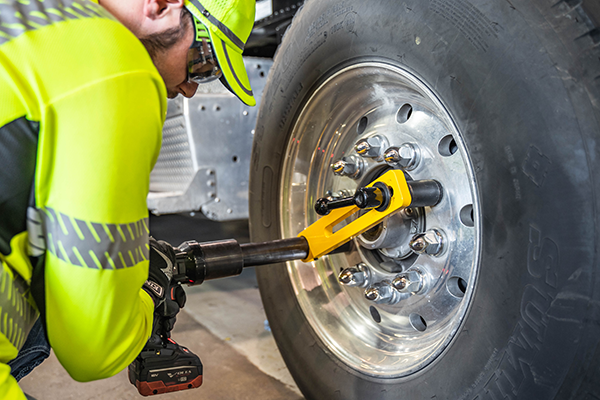
Rust streaks on the surface of your rim are a tell-tale sign of loose lugnuts and possible issues. Make sure you keep your lugnuts tight and secure by properly torquing them to manufacturer specifications. Correct torque settings prevent tire, axle and bearing wear, especially following a hub service or the arrival of a new trailer.
When mounting a set of tandems, be careful not to damage the wheel studs and make sure the valve stem for the inner wheel is accessible from the outside wheel hole. Tighten the nuts by following an alternating criss-cross pattern to an initial setting of 50 ft.-lbs. Once the wheel set is snug, torque the lugnuts to the final setting of 450-500 ft.-lbs. following the same rotation.
2. Hub inspection
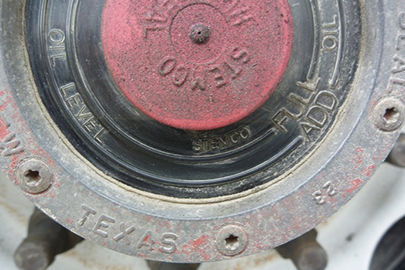
Similar to wheel torque settings, you should also take a good look at the hub.. According to manufacturers like Landoll, the wheel end contains the most “consumable service items.” Major repair costs can be occurred when components are not maintained and serviced properly.
During your visual inspection, make sure the hub oil is at the recommended level on the sight glass and fill accordingly. Excessive hub temperature is a sign of poor lubrication and low oil levels. During your pre-trip, be sure to look for oil leaking on the inside of the rim and on brake components.
You should also keep an eye out for loose, damaged or missing fasteners. If you discover any, put the trailer out of service if any of these defective conditions are present.
3. Suspension overview
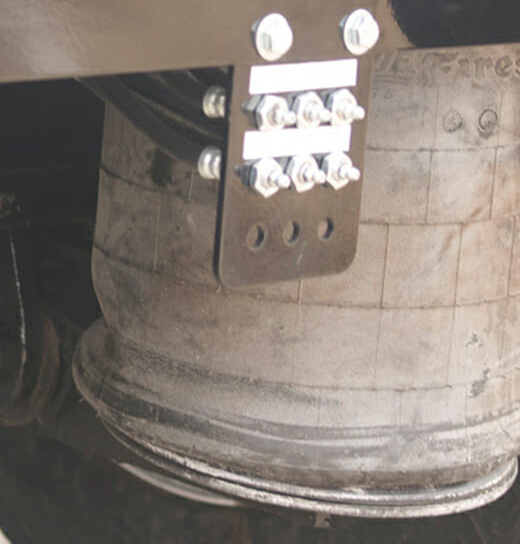
While still under the trailer, proceed next to suspension components, once again looking for loose, cracked or broken parts and verifying torque specifications on all nuts, bolts and fittings. Air bags should also be inspected for equal firmness, and leaf springs should be scanned for cracks. Refer to the trailer manufacturer’s manual for further instructions.
4. Tire alignment
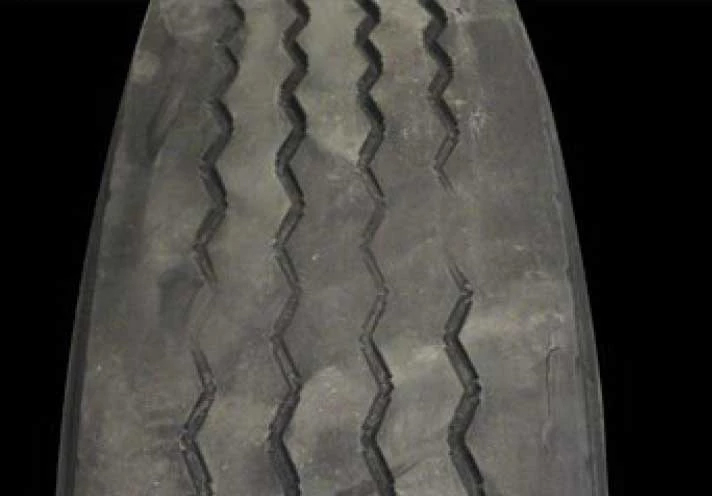
After looking at your trailer’s lugnuts, wheel bearings, hubs and suspension, take a minute to check the tire pressure and the wear patterns on your trailer tires. Many industrial trailers offer tire inflation systems to maintain tire pressure. A quick check with an inflation gauge will prevent a roadside repair farther down the highway.
If you see signs of uneven tread wear, notify shop personnel. The trailer may be out of alignment or may be suffering from a damaged suspension or axle component. Scuffed tires or tires with feathered edges could be a sign of negative camber and should be addressed by certified technicians.
According to trailer manufacturer Landoll, proper axle-to-kingpin alignment is “necessary to obtain straight tracking.” If axle alignment is off, “dog-tracking” occurs. Check alignment manually or with a semi trailer alignment machine. A thorough inspection of the complete suspension system must be performed, and all defects need to be corrected before alignment.
5. Brake systems
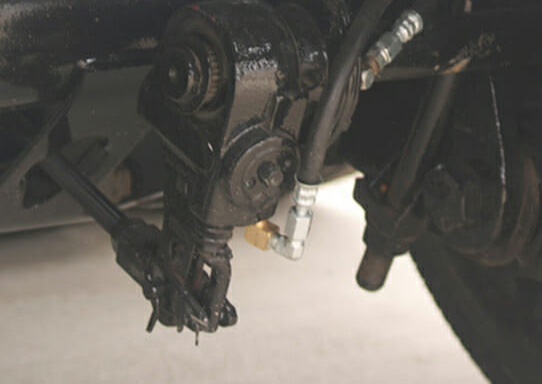
The importance of stopping your trailer needs little explanation. Whether equipped with drum or disc brakes, daily brake inspections on your trailer need to be part of your dispatch routine. Most out-of-service tickets are related to brakes being out of adjustment, and most roadside DOT inspections are looking for brake system violations. Don’t risk an out-of-service ticket.
At a minimum, manufacturers like Landoll recommend trailer brake systems be inspected every 500 miles. Drivers and technicians should be looking for chafing air lines, hose kinks and damaged fittings. Keep an eye out for loose, missing or corroded fasteners. As always, any defects discovered should be fixed before the trailer returns to service.
Brakes need compressed air to operate, so make sure your power unit’s compressor is in operational condition. The gladhands should be sealed with plumber’s tape and the rubber grommet insert is not missing or deformed. Always remember, audible air leaks do not pass inspections.
To prevent ice build-up in air lines, be sure to drain the air reservoir daily. A drain cock is located on the bottom of the reservoir and allows collected water and oil to drain properly and exit the system before problems develop. Once complete, make sure the cock is sealed tightly to the bottom of the tank.
6. Hydraulic system
Your industrial trailer needs uninterrupted hydraulic fluid to function properly. Make sure you keep your tractor’s wet kit free of debris and water so fluids can flow freely without restriction. Start with a 10-micron filter and regular service changes. A well-maintained system will keep your trailer working as it should when you need it to.
Just like your semi’s engine oil, be sure to check the hydraulic oil level daily and look for signs of fluid contamination. Evidence or presence of foreign materials can clog your system and may require a full-system flush. Don’t let debris stop you in your tracks when you are in the middle of a delivery.
7. Deck condition
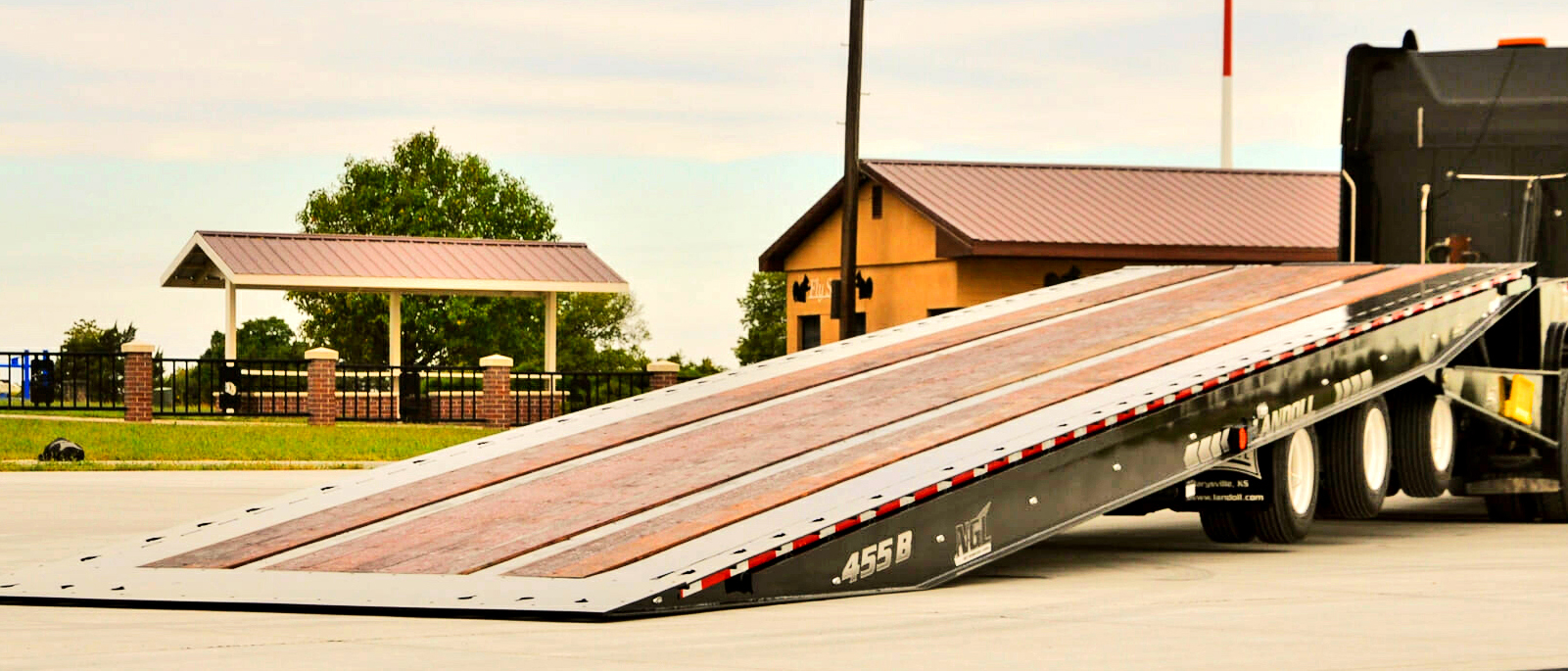
It’s hard to haul flatbed freight with a compromised deck surface. Whether your trailer’s deck is made from wood, metal or a combination of both, inspect for loose sections, missing fasteners and other surface defects. Over time, the condition of your trailer’s deck can suffer from loading abuse, road vibration, weather elements and repeated washing.
If primarily wood, the best way to prolong the life of your deck is to treat the wood annually with preservatives. A deep penetrating oil-based formula that repels moisture will pay itself back over time. Check with your local home improvement store or
refer to the can for application instructions. Periodic recoating could prevent deck failures in the future.
8. Electrical connections
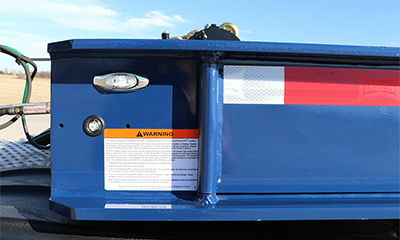
The mark of any good pre-trip inspection is working lights on both the tractor and trailer. How many times have you seen a tractor-trailer heading down the highway with a burned-out headlight or clearance light? Did the driver actually perform
a walkaround inspection?
Don’t get trapped by apathy. Make sure you do your job. Just remember, if a light is on your trailer, it needs to work.
Faulty trailer lights are just the beginning of your trailer’s electrical inspection. Always check the seven-pin connection to the trailer and ensure a solid fit. The cord end should be free of debris and bent or loose pins. Additionally check for, any wire, electrical connection or electrical component showing signs of corrosion, wear, breakage or unraveling.
9. Roller and wear pad inspection
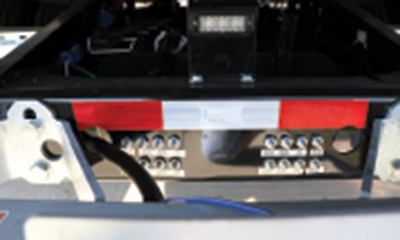
If your industrial trailer features a traveling axle setup, make sure you inspect the rollers and wear pads located on the undercarriage. These key components must be properly maintained to ensure smooth axle travel. If a bearing is seized and
not rolling freely on the main beams, the roller could suffer a flat spot and require replacement, causing additional cost and downtime.
Landoll recommends lubricating rollers monthly or every 2,000 miles. Refer to your trailer owner’s manual for grease zerk locations and scheduled maintenance intervals. Wear pads need to be replaced any time unusual wear appears, compromising
bolt heads and mating material.
10. Dock leveler maintenance
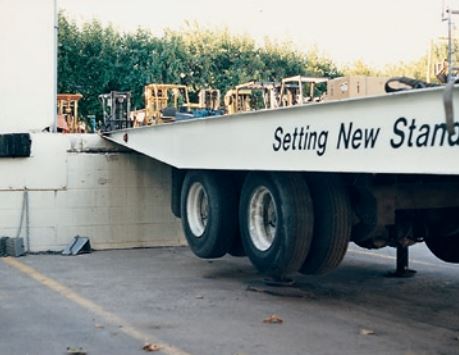
Lastly, dock levelers round out our list of inspection points on your industrial flatbed trailer. Typically located between the rear axles, these dropdown legs provide support while loading equipment from a ramp or dock and prevent unnecessary suspension
damage. Before moving a trailer, always make sure the legs are in the raised position for transport.
Daily use of leveler’s legs keeps the system fresh, but if your cylinders are seldomly used, you should still cycle the legs up and down at least weekly so oil circulates through the lines. This extra step ensures the leveler’s legs are ready
and available when you need them.
Leveler legs should always be in the retracted position prior to transport. During your pre-trip inspection, you should check for loose, missing or damaged hardware. You should also look for hydraulic leaks and any unsupported lines that may be damaged.
If any unsatisfactory conditions exist, put the trailer out of service for repair.
We hope you find this list useful. Always refer to your trailer’s owner’s and service manuals for exact details and instructions. Inspection points may vary by manufacturer, but the intent here is to not skip a step.
Once again, drivers and
fleet managers need to remain mindful of all the moving parts on a trailer. Keeping your trailer in its best shape is in everyone’s best interest.
Having the products and equipment that you’d need to inspect your trailer on-hand can
be the difference between performing these inspections or not. Be sure you have the supplies you need by visiting our Auto & Truck Service department.