by
Cameron Hanson
| Aug 18, 2023
Eleven-year-old Jace Tapp dreams of playing in the NFL someday. If that doesn’t work out, his fall-back plan is to follow in the family towing business. Sounds like his dad will save a spot for him at Central Iowa Towing and Recovery.
In fact, there’ll be room for everyone in the family if that’s what they want to do when they get older.
“We have four children, and they have all been very active in this business, ever since they could walk, really,” patriarch Dustin Tapp said. “I would hope in 20 years that they would all want to be involved
in this business, and I would love it if they could take it over. That’s not 100 percent my decision, but it’s definitely my goal.”
A native of Nevada, Iowa, Dustin started Central Iowa Towing with his wife, Rickie, in 2014. Then 28, he had previously worked as a mechanic in nearby Ames, where he was first exposed to the profession, responding to accidents
and breakdowns within a few weeks on the job. He said the decision to branch out on his own was by “accident,” pun intended.
“I kind of fell in love with towing and started managing and growing that side of the business where I was working,” Dustin said. “I then reached the point where I wanted to do my own thing and bought my own truck. We started out with
one rusty old tow truck out of a run-down, old farmhouse by Nevada, and it’s kind of escalated from there.”
In less than 10 years, the Tapps have grown Central Iowa Towing into one of the largest towing and recovery businesses in the state. Based in Ames, the company operates two locations there and has expanded into the Des Moines and Marshalltown
markets. They also recently partnered with a towing company in Waterloo.
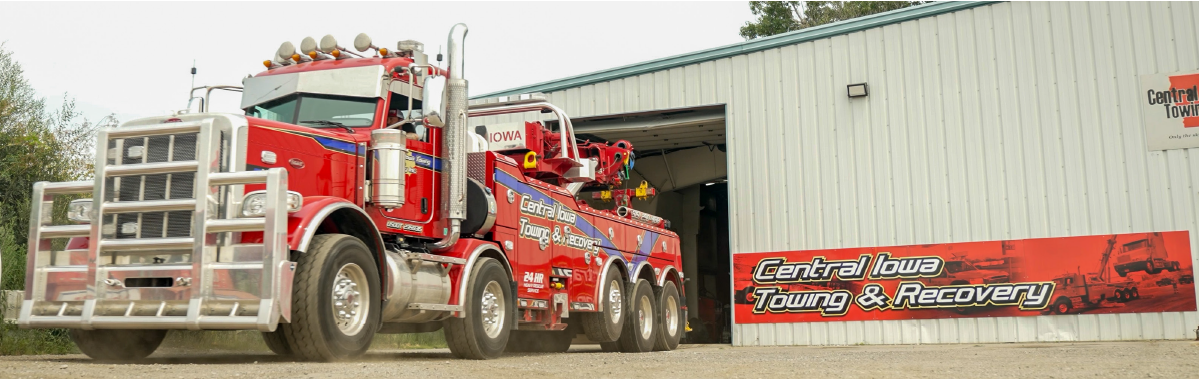
Serving the heart of Iowa, their fleet consists of heavies, car carriers, light-duty wreckers and mobile service vehicles. The family favorite, according to son Jace, is the Century 1150 twin-steer rotator. Strategically located by Interstates 35 and
80, the crew stays busy responding to rollovers, breakdowns and weather-related incidents, including a 70-car pileup one winter.
“We can do everything from your small car lockouts to tractor-trailer rollovers to underwater recoveries,” Dustin said. “We can do just about anything you can think of. I hope we’re remembered as providing the total package...that
when our guys showed up, they got the job done.”
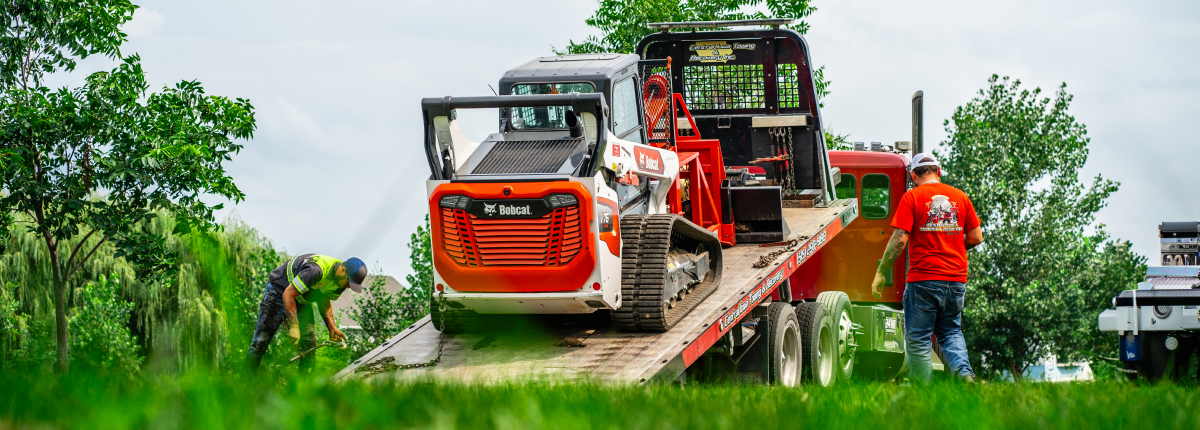
“Central Iowa Towing is different because we take pride in what we do,” Rickie added. “Our trucks are clean, and we put a lot of effort into making sure our employees are taken care of.”
The Tapps credit their team of operators, dispatchers and mechanics for the company’s success and solid reputation. Among those dedicated employees is Bailey Metzger, who has served as the company’s dispatch manager for the past three years.
She makes sure all calls get routed correctly and in a timely manner.
“I monitor all the calls that come in to make sure we’re getting accurate information for every call,” she explained. “Over time, you learn what information we need for certain situations. Once you’ve been through those scenarios,
you remember what to do the next time.”
“The most challenging aspect of running this company is managing employees,” Dustin admitted. “One of the best ways to manage our growth is by hiring the right people and trusting those people to do their job. I definitely
went through a period of being a micromanager. It took me a lot to release everything, but once I did, it was the best thing I ever did.
One of the best ways to manage our growth is by hiring the right people and trusting those people to do their job.
—Dustin Tapp
“We’ve been fortunate enough to hire some really good people and put them in the right places,” he continued. “But it’s tough nowadays trying to find young adults who want to put in the physical labor.”
Hoping to buck that trend, the Tapps eagerly involve their children in the family business, and leading by example, they hope to pass their work ethic on to the next generation. Besides Jace, the family includes eight-year-old daughter, Carson; oldest
son, Gage, 16; and youngest son, Cade, 6. Although still school age, the Tapps’ children help out when and where they can.
“I enjoy coming to work and talking with all the people here,” Gage said. “I help with washing trucks, and when I get older, I plan to continue to help my dad in the business.”
“My dad is my biggest role model because he is a really hard worker, and he’s built this business in a short amount of time. He has come a really long way,” Jace added.
Bailey said the “family atmosphere” is what she enjoys most about coming to work every day at Central Iowa Towing. “You get to have fun all day. It’s really not stressful at all,” she said.
Rickie said working together as a family has strengthened their bond both professionally and personally.
“Most proud, I would say, is seeing how Dustin and I have grown together,” she said. “Working with your spouse isn’t always easy. There have been ups, and there have been downs. Our relationship has really grown
just by learning things that we basically have had to figure out on our own.”
Besides the commitment from their employees and the support from their family, the Tapps said they also appreciate the response they’ve received from the communities in which they serve. To return the favor, they believe in giving back and regularly
support school activities and community organizations by volunteering and giving donations and sponsorships.
“There were plenty of other wrecker services when I started, but our home community, as a whole, took a chance on us, and I feel the best thing to do is to give back,” Dustin acknowledged.
The Tapps said they are also grateful for their relationship with Zip’s AW Direct. Their company has been a loyal customer of Zip’s since they started, and whenever possible, the Tapps continue to purchase trucks, apparel and gear from their
fellow Iowa-based company. Service before and after the sale also goes a long way, and first impressions make the difference.
Nearly 10 years ago, “I walked into Zip’s with nothing to my name and told them I want to start a towing company. They took a big chance on me and let me drive a truck home that day with almost no money down,” Dustin said. “That’s
one of the reasons why we are so loyal to Zip’s because they gave me a shot when nobody else would.”